一、计算机配料控制系统
(一)、系统组成:
本控制系统由称重计量装置、检测元件、控制执行机构以及工业计算机等组成,称重计量装置是动态工作方式的调速皮带(或调速螺旋、调速链板等)定量给料机包括变频电机),检测元件是指称重传感器、速度传感器及信号放大器,控制执行构包括数字计控仪表,PLC控制器以及变频控制器等,计算机采用存贮容量大,运行速度快,扩充灵活的高性能工业主机。由此组成了一个功能完善,性能稳定,运行可靠的控制系统。
(二)、主要技术参数
1、动态累计误差:≤±0.5%,≤±1%
2、流量调节范围:≥10:1
3、物料:任何颗粒状及粉状
4、粒度:≤50mm
5、水份:不沾皮带为限
6、容重:0.7~1.5t/m3
7、使用环境
a、工作温度:-20℃~+50℃
b、相对湿度:≤85%
8、 控制路数:多路(无限制)
(三)、系统功能
1、零位自动校正去皮重;
2、任意设置皮带秤工作台数及被测物料名称;
3、各物料流量定值控制;
4、物料总量调整及控制;
5、手、自动无扰动切换;
6、物料堵料和喷料超限声、光报警;
7、经报警延时后,自动切断全部皮带秤电源;
8、参数和数据自动存盘,长期保存;
9、自动检测A/D输入信号,发现故障自动退出‘运行’状态;
10、具备通讯接口及软件实现联网;
(四)、工作原理
该系列变频调速皮带定量给料机与工业控制计算机联机使用,料仓出料口通过法兰与调速定量给料机上的接料斗直接相连,物料从料仓出料口随着皮带的转动被均匀地分布在皮带上而缓慢地出料,物料的重量通过皮带及称重框架传递到荷重传感器上,将此重量信号转换为电信号,经放大器输出标准电压(或电流),并与定量给料机传动部分测速传感器输出的速度信号(转换为相应电信号)相叠加(俗称A/D),计算机在一定周期内连续采样,此信号经计算机处理后得到实际流量,将实际流量与所设定的流量相比较,计算机利用差值通过变频控制器不断地调整皮带速度(俗称D/A),从而达到定量配料与连续计量的要求,本系统中计算机可以控制多台调速皮带秤同时进行配料。也可以采用一台计算机同时控制二条配料线。
系统组成和系统工作原理框图如下所示:
二、PZW-D复合肥喷浆造粒及配料全自动控制系统
(一)、尿素熔融喷浆造粒工艺及控制流程图
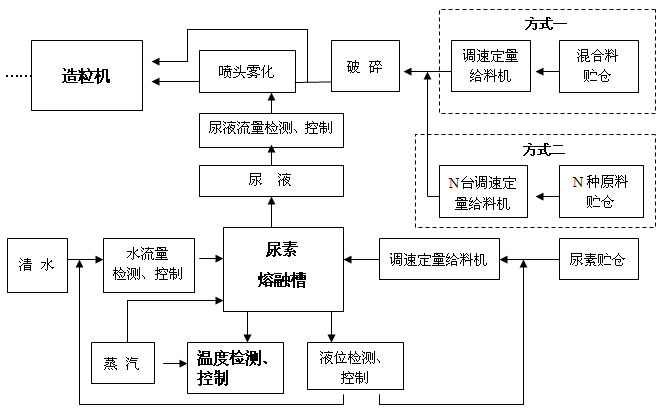
1、图中虚线内方式一与方式二是二个不同的配料方式,采用其中一种方式就可。
2、方式一是多种原料由人工配料,然后用一台调速定量给料机通过计算机控制混合料进入造粒机的流量。
3、方式二是多种原料由计算机控制多台调速定量给料机,按工艺配方要求进行自动配料,然后再由计算机控制进入造粒机的总量。
(二)、控制系统组成及主要功能
本系统由四部分组成:监控计算机、传感检测机构、智能仪表、和输出执行机构;
1、监控计算机:监控计算机为工业PC,配有UPS,打印机等辅助设备。计算机的操作系统Windows xp,应用软件采用Delphi语言开发,为用户提供了良好的界面和强大的数据库管理功能。监控计算机的主要功能为:
(1)工艺过程参数监控;
(2)运行参数调整、备份;
(3)操作人员管理;
(4)配方管理;
(5)产量管理并以报表的形式输出到打印机;
(6)历史消息管理,包括操作消息,报警消息等;
2、传感检测机构:传感检测机构快速准确把重量信号、转速信号、温度信号、液位信号等转换成电信号,主要的信号为:
(1)原料定量给料机的重量和速度信号;
(2)尿素定量给料机的重量和速度信号;
(3)水流量信号;
(4)尿液流量信号;
(5)熔融槽内尿液的温度;
(6)熔融槽内尿液的液位;
3、智能仪表:智能仪表采集各传感检测机构送来的电信号后计算出实际值,同时仪表根据用户的设定值自动计算执行机构的输出值并转换成电信号。仪表为中文界面,防尘防潮设计,能良好的适应复合肥生产的环境;仪表的主要功能为:
(1)各种流量、温度、液位等信号的闭环调节控制;
(2)方便的查阅、设定运行参数;
(3)方便的整定、调整参数;
(4)声光报警;
(5)带RS-485 接口和监控计算机交换数据;
(6)带有远控接口可以方便的和PLC连接。
4、执行机构:执行机构的功能是快速准确地调整到仪表的输出值,从而使实际值和用户的设定值相符合,系统的执行机构为:
(1)原料定量给料机:变频调节转速;
(2)尿素定量给料机:变频调节转速;
(3)水流量:模拟阀门调节;
(4)尿液流量:尿液泵变频调节;
(5)熔融槽内尿液的温度:模拟阀门调节。
(三)、系统特点:
1、工艺特点:本工艺与传统团粒法工艺最大的区别在于它是以尿素料浆作为液相,代替蒸汽造粒。其成球率,产品质量,产量均能显著提高。另一方面,物料含水量低,烘干温度大大降低,产品水分低,品质高。同时保留了原有工艺路线,使广大传统团粒法工艺老厂能在原有生产线的基础上用最小的投入获得最大的收益。
2、改善企业产品结构,特别是提高高氮产品的多样化,满足不同的市场需求。
3、采用尿素喷浆造粒工艺可以显著地改善成球率,降低对原材料的要求,提高产品的产量。
4、产品粒度均匀,圆润光滑,水份适度,不宜结块,提高了产品质量。
5、和其它造粒工艺相比,尿素喷浆造粒工艺投资少、工艺简单、操作方便。
三、PZW复合肥生产过程自动控制系统
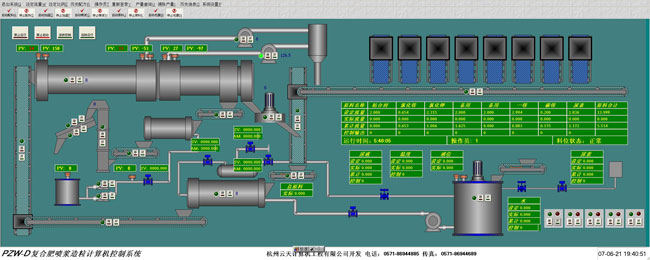
在复合(混)肥生产领域,利用电子计算机技术,对局部生产环节或整个生产过程进行自动控制,这个工作起步较晚,整个行业自动化水平还是比较低的。随着电子计算机技术的日新月异,人们对应用该技术的热情也日益高涨。
根据复合肥生产工艺过程,计算机控制主要可分为以下几个方面:
一、原料配料控制
二、喷浆造粒控制
三、热风炉烘干控制
四、成品包膜控制
五、包装计量控制
六、系统工艺流程控制
上述控制均采用集中-分散型模式,也就是检测控制功能分散化,监视操作管理集中化。一级分散检测控制由单回路智能仪表执行,二级集中监视操作由工业计算机完成,仪表与计算机之间采用通讯方式联机。进行数据传送及优化处理。这种模式的控制系统其最大特点是:
1、组态灵活,扩充方便。
2、性价比高,运行成本低。
(一)、原料配料控制
以变频调速皮带秤配料控制为例。
1、控制系统组成
系统由多台调速皮带秤、称重传感器、放大器、速度传感器、变频控制器、智能计控仪表及工业计算机组成。系统主要设备――调速皮带秤是一种新型的电子动态计量装置,在引进国外技术(德国申克)的基础上,针对复混肥生产工艺及现场特点,进行了必要的适当改进。选用部分防腐材料,整体经过防腐处理,主要部位密封性好,防尘抗腐性强。关键部件采用国外原装进口,能在腐蚀性环境中长期稳定可靠地工作。
2、控制原理
调速皮带秤的接料斗直接与原料仓的出料口通过法兰连接在一起,每一种原料都各自配备一台调速皮带秤。通过计算机或仪表按工艺配方要求,设定每一种原料的配比(或流量)。工作时,原料从料仓出口经接料斗,进入到皮带上,随着皮带的转动,原料被均匀地输送出来。皮带上的物料重量和皮带运行的速度量经相关的传感元件检测后,输入到智能仪表及计算机,进行叠加处理,一方面显示出各种流量参数,另一方面把实际流量与设定流量不断地进行比较,根据差值通过变频控制器随时调整皮带速度,使每一种原料都能按照设定的流量控制,从而实现自动定量给料和连续计量,组成一个多回路(一般在12路以内)的配料自动控制系统。系统同时建有强大的数据库,能方便地查询三年以内的产量(班产,日产,月产,年产);流量(累计、设定);配比以及修改配比的时间和运行时间;报警次数和时间等等。
(二)、喷浆造粒控制
以尿素熔融喷浆转鼓蒸汽造粒控制为例
1、系统组成
控制系统由尿素调速皮带秤、水流量计、温度检测仪、液位检测计、尿液流量计、混合料调速皮带秤、水调节阀、蒸汽调节阀、尿液调节泵以及智能计量控制仪表和工业计算机组成。系统有手动控制、单回路自动控制和多回路全自动控制方式,确保了在恶劣环境条件下连续生产的稳定性和可靠性。
2、控制原理
首先根据工艺要求通过计算机或仪表设定有关配比及参数,由尿素调速皮带秤上的称重传感器及水流量计(电磁流量计)的一次仪表将信号转换后,通过计算机或仪表分别取得进入熔融槽内尿素和水的实际流量,并与设定的流量相比较,根据差值不断调整调速皮带秤的速度和水调节阀的门开度,使尿素和水按比例自动进入熔融槽内(尿素和水的比例一般为100:5)。同时又根据熔融槽内的液位计的检测信号,瞬时调整进入熔融槽内尿素和水的总量,使熔融槽内的尿液液位保持在一定的高度范围内(一般控制在满度的65~85%之间)。其次对熔融槽内的尿液温度进行检测,并与工艺要求的温度值进行比较,通过计算机或仪表自动调整蒸汽调节阀的门开度,使尿液温度控制在允许变化的范围内(一般要求尿液的温度在115~125℃之间)。再则对进入造粒机的混合料和尿液的流量分别通过调速皮带秤和电磁流量计进行检测,获得各自的流量信号,同时根据工艺配比要求,由计算机或仪表自动调整调速皮带秤的速度和尿液泵的转速,使混合料和尿液按比例同步进入造粒机内,最终达到工艺配方的要求,生产出符合质量标准的复混肥。本系统中温度的控制是最关键的环节,若温度高了,缩二脲含量会超标,施肥时容易烧苗;反之温度低了,达不到熔解效果,易发生喷头堵塞,造成流量不稳定,影响产品的品质和产量。
(三)、热风炉烘干控制
以沸腾热风炉烘干为例。
1、控制部分组成
检测部件包括:热电偶、热电阻、压力变送器等。
执行机构包括:电动调节阀、圆盘调速喂煤机等。
控制部分包括:智能控制仪表及工业计算机。
2、控制原理
工作时,燃煤经圆盘喂料机匀速地送入炉膛内,炉膛温度和烘干机进口温度以及出口温度分别由热电偶和热电阻检测。一般正常工况下,烘干机的进料量和进料的水份是一相对稳定值,当出料水份偏大时,烘干机的出口温度就会偏低(说明这时候要加温),热电阻检测到此温度信号后经仪表传送给计算机,计算机经数值比较后,再通过仪表输出控制信号,一方面加快圆盘喂煤机的转速,增加给煤量;另一方面调整电动调节阀门一,加大燃煤鼓风机的风门,也就是增加风量,以保证过量氧气供给和维持系统的正常燃烧温度,同时调整电动调节阀门二,加大射流风机的阀门,进行冷风补给,从而保证烘干机的进口热风温度(125~150℃),经以上调整后,烘干机的尾气量也会增加,这时为了确保系统负压供热气流的畅通,应适当调大尾气引风阀位的开度,增加引风风量,反之一样(出料水份偏小――烘干机出口温度上升――减少喂煤量――减小燃煤风机风量――减小射流风机风量――调小尾气引风风量)。经过这样的不断调整,使得烘干机出口物料的水份能控制在一个比较理想的范围内。系统中除了以上的检测、控制点以外,燃煤风机工作状态的正常压力以及炉膛正常燃烧时的负压力也是本系统比较重要的检测点,因为控制热风炉的正常燃烧温度,除了风、煤量的合理调配以外,还必须要求炉膛温度与炉膛负压能稳定在一个正常的、微小的偏差范围内,以保证系统负压供热气流的畅通。
值得一提的是,以上的控制模式是建立在运行参数基本稳定的基础之上,也就是说当燃煤的品种是一定的,进烘干机的投料量也是基本稳定的,在此基础上对以上关键参数进行自动控制调节,否则就不能用这种常规控制模式。
(四)、成品包膜控制
1、控制系统组成:
包膜控制部分由半成品调速皮带秤,包膜油罐,包膜油泵,包膜油流量计,包膜粉仓,包膜粉秤,以及成品料仓料位控制器等部分组成,工艺流程如下:
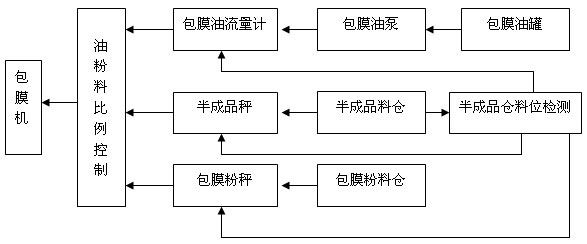
系统按检测的半成品料仓的料位情况,当料仓料位接近空仓时,包膜系统停运。当料仓接近满仓时,自动启动包膜系统。结合料位高低,自动控制进包膜机的流量,流量分为大流量,中流量,小流量,包膜系统运转中的油粉料始终按设定比例投入包膜机,保证包膜系统的包膜成本和效果。此系统很好地解决了传统包膜系统半成品来量不稳定造成的包膜成本高,效果不佳,非多即少的现象。
2、主要技术参数:
包裹油精度:≤±1~2%
包裹粉精度:≤±1~2%
半成品精度:≤±1%
(五)、 包装计量控制
以单仓自动包装机为例。
1、组成
自动定量包装机是由气动进、卸料阀门;气动夹袋装置;称量斗;称重传感器以及智能计量控制仪表等组成。这是集机、电、仪、气为一体,自动化程度较高的一个计量产品,它的机械部分全部采用不锈钢材料,结构设计为全密封。智能计控仪采用高性能、高速度的微处理器。A/D精度16位,薄膜面板,塑料外壳,防水接头,称重传感器是由美国梅特勒技术生产,整台设备结构新颖、体积小、重量轻、包装速度快、精度高、稳定性好。
2、控制原理
工作前先设定要控制的袋装重量和快、慢进料的工作时间以及一些相关参数,由智能计控仪表自动检测去皮重,使显示为零。工作时,在套上袋子接通接触开关后,智能计控仪表自动开启气动夹袋装置,随即将气动卸料阀门自动打开至最大位置,开始快速下料,当接近设定值时,卸料阀门自动切换到慢速下料位置,最终达到设定值时,自动关闭卸料阀门,待显示值稳定延时后自动打开夹袋装置,掉袋后由输送机送至缝包,完成一个装袋过程,下次工作时重复以上过程,不断循环。操作简单,使用方便。
(六)、系统流程控制:
系统采用SIEMENS公司S7-300系列CPU,系统流程控制部分,包括所有设备的逻辑起停,大功率设备(如烘干机、造粒机、冷却机)的电流电压监测,烘干机头尾温度检测,冷却机头尾的温度检测,烘干机头尾负压检测,冷却机头尾负压检测,造粒机出口温度、湿度检测,包膜油温度监控。
复合肥系统中相对的测点规模较小,逻辑关系也相对简单,主要实现的功能如下:
1、电机过流,过载,过欠压保护;
2、所有设备顺序启动、停止;
3、禁止启动,禁止运行等保护模式;
4、设备运转状态监控,保护停止时报警,(可选择全设备顺序停车);
5、烘干机头部尾部温度、负压检测;
6、冷却机头部尾部温度,负压检测;
7、造粒机出口温度湿度检测;
8、包膜油温度监控。
系统画面,根据系统工艺流程完全在画面上展现,系统采用多屏幕操作,即一台操作站上配置2台以上显示器,操作员的手不需要离开鼠标,便可以在两副以上的画面上进行操作,系统操作简便,功能强大,数据报表完整,操作记录信息全面,历史操作记录、历史报警记录查询方便。
将上述若干个控制过程通过现场总线及通讯方式可组成一个高性能分布式的集散型控制系统(DCS控制系统),即复合肥生产过程控制系统,它包括了对所有设备的实时监控,这是化肥工业实现集约化,规模化的必然趋势。
四.水泥厂生产过程自动监控系统简介:
(一)、水泥生产工艺主要控制对象
水泥生产工艺过程主要包括:
原料及生料预均化――生料配料――生料预磨及细磨――回转窑烧成――熟料配料――水泥细磨――成品出厂(散装或包装)
与上述工艺过程相对应的主要控制环节是:
1、原料及生料预均化控制:
一般采用分别堆放、多点进料以及采用NG型连续式均化库,利用变频调节空气搅拌方式。
2、生料配料控制
生料配料控制一般采用质量跟踪控制法(率值控制),是由多回路计量装置与在线分析仪相结合,利用自动取样机进行动态物化分析,对其配比实行自动调节和跟踪控制。
3、序磨及生料磨监控
采用对辊压机及生料磨的负荷状况以及出磨物料细度和返料的在线检测,控制入磨总物料量,使辊压机及生料磨达到平稳,高产的最佳运行状态。
4、回转窑烧成监控
窑系统是由废气处理、生料喂料、预热器、分解炉、回转窑、冷却机和窑喂煤等组成。通过对气流量、物料流量,燃烧量,温度,压力等工艺过程参数的实时检测和控制,使一个具有复杂的多参数。多变量的烧成系统变为相互协调,有机配合的一个整体。
5、熟料配料控制
一般采用多回路重量配比法,利用多路称量装置,对多种物料进行连续动态配比调节控制。
6、水泥磨监控(与生料磨相似)。
7、散装水泥发放控制。
利用单只或双只静态计量仓,对进、出料量进行控制,通过气力输送或机械输送装置,根据事先设定装载量,将散装水泥直接装船或装车(火车、汽车)。
(二)、DCS控制系统简介:
水泥厂DCS系统是利用多微处理器,将控制动能分散,把一系列现场控制装置分散到不同生产过程区段中去,在中控室设置集中操作监视及上位机,与各现场控制装置通过数字通信与其相连,进行数据与信息交换。在中控室内有大型CRT显示和打印机,通过键盘可方便地调出各种画面和打印数据,操作人员根据形象的画面显示,改变各控制回路的设定值,运行工况,整定参数及回路结构,从而实现对整个生产过程的自动控制。
DCS控制系统具有以下特点:
⑴、系统智能化
⑵、控制分散化
⑶、操作集中化
⑷、组态灵活化
⑸、网络通讯化
1、系统硬件组成:
本DCS系统配置1个工程师站(可兼操作员站),3个操作员站,4个现场控制站。
工程师站和操作员站配置DELL Precision 380工作站,配置双显示器,鼠标键盘,工程师站配置一台打印机,其中一个操作员站培植一台打印机,两台打印机地位平等,互为冗余,可执行系统所需全部打印任务,每个现场控制站由一台主机柜和若干台扩展柜组成,主机柜安装冗余的一对控制器,冗余的分布式电源模块,以及若干I/O模块,扩展机柜安装冗余的分布式电源模块以及若干I/O模块,控制器和I/O模块之间通过PROFIBUS-DP总线连接。操作员站和现场控制站之间通过冗余的100兆工业以及太网连接,全部到现场信号均配置安全栅,安全栅和I/O模块之间采用混合安装方式,在机柜背面安装SIS系统。
2、 软件组态
本项目的软件组态是使用WINCC系统软件平台提供的功能和手段来实现组态标准包的应用要求,软件组态有以下几个特点:
⑴、全部操作以面板为中心:不同的类型的仪表具有不同的操作面板,在些操作面板里完成对仪表相应的全部监视和操作,对与需要操作的设备所有信息,状态,功能,使用指南,在一个控制面板内完成。
⑵、面向对象思想的应用:在系统组态中,贯穿了面向对象的思想,操作员看到的仪表位号已经不是一个单一的仪表位号,他看到的是一个仪表设备,和此设备相关的一系列信号状态,质量状态,以及与次设备相关的一系列操作和动作。
⑶、系统支持多国语言功能:系统支持多国语言显示,多语言可以在线任意切换,不需要退出系统,语言支持的范围是WINDOWS操作系统所支持的全部语种。
⑷、多屏幕操作:是一个操作员站上配置2台以上显示器,操作员的手不需要离开鼠标,便可以在两副以上的画面上进行操作。
⑸、丰富的自诊断功能和电子维护指导:系统具备从系统到模块的I/O通道级的自诊断功能,提供了丰富的自诊断信息,方便维护,同时,系统提供了形象的系统运行状态图,另外还提供了电子接线图,电子维护指导手册。
⑹、适合行业特点的流程图、控制回路及人机界面:系统流程按照两级别组织方式,即:主总貌图和子总貌图。
⑺、丰富的报警查询,全日志查询功能:按报警类别:高高限、高限、低低限、低限;开关量、模拟量;区域;系统报警,工艺报警;按名称;按日期和时间;查询信号短路,断路,超电量程上限,超点量程下限等列表。
报警信号的状态图标显示:报警发生未确定未消失,报警发生已确定未消失,报警发生未确定已消失,报警发生已确定已消失。
报警发生的原因,发生的时间,确定的时间,消失的时间,确定理由,确定人员等信息显示。
详尽的日志:操作员站名,时间人员,位号,操作结果等。
系统全部日志分类查询,按操作员站名,时间人员,位号。
水泥生产过程检测与控制系统中,变量参数关联度高,连锁控制逻辑非常复杂,生产过程控制要求极高,复杂的高级控制算法及计算量大;DCS系统具有开放的接口,易于接到第三方系统以及具有强的组网能力,消除信息孤岛,运行稳定,可靠,效果良好。
3、系统配置原则
冗余原则:控制器、通讯总线、网络、电源等关键设备均采用1:1冗余
余量原则:对于I/O测点、硬盘、机柜空间等均按照用户要求配置满足要求的余量。
负荷原则:对于控制器负荷、处理能力等技术参数按照要求负荷配置。
完整原则:系统的配置符合用户技术规格书要求以及相关文档要求。
五、SJK-IV散装水泥输送计算机计量控制系统
(一)、概述:
电子料斗秤是新型计量控制装置,它适用于在码头、矿山、堆场等场合,对固体散装物料的流量计量和控制。它可以对物料进行连续式或间断式的计量控制,具有计量精度高、流量范围大、密封性好、可靠性及稳定性高、价格低廉、使用寿命长、故障率低及维护操作方便等优点,受到广大用户的欢迎。
(二)、产品结构及组成:
电子料斗秤由称量斗,气动卸料阀门,称重传感器,放大器,PLC控制器及工业控制微机组成。是集机、电、仪、气合为一体的自动化程度较高的产品。
机械部分的计量仓可以设置一台或双台,机械动作的执行机构由气、电结合,通过计算机及PLC控制器实现全过程自动控制,能在粉尘大,工作环境差的情况下,长期可靠工作,而且安装方便,调试简单。
计算机采用最新工业控制计算机与PLC控制器,作为料斗秤的核心部分,对物料流量进行瞬时检测,反馈控制,信息处理,数据存贮,显示及打印。气动进、出料阀门作为料斗秤的执行机构,对进、出物料进行控制,称重传感器及放大器是料斗秤的关键器件,它直接关系到料斗秤的精确度,稳定性及可靠性,输入及输出信号均采用通用的标准电信号,为便于设备的维护使用,设置了手动及自动控制二种方式。在正常工作状态下,采用自动模式;在异常或调试维护状态下,采用手动模式。这样可大大提高料斗秤的使用率,始终保持最佳工作状态。
(三)、主要技术参数及功能:
1、主要技术参数:
⑴、称量范围:50t/h、100t/h、200t/h、300t/h。
⑵、累计误差:优于±0.5%
⑶、称量方式:连续式,间断式(双仓式,单仓式)
⑷、适用物料:粉状,颗粒(无粘性)
⑸、供气压力:0.7Mpa
⑹、供气电源: 220V±10%
50HZ±1HZ
⑺、工作环境:温度:
计量仓:-20℃~60℃
控制部分:-5℃~35℃
湿度:≤85%
2、功能
⑴、自动去除皮重,零位校正;
⑵、参数设置及修改;
⑶、数字标定自动修正误差系数;
⑷、数据存贮,掉电保护;
⑸、大屏幕显示各种数据及打印;
⑹、故障报警及自动连锁动作;
⑺、手-自动无干扰切换;
⑻、具有与上位机通讯联机接口。
(四)、工作原理
具体的工作过程为:首先通过键盘对所需流量范围的有关参数进行设置或修改,放空计量仓,一次去除皮重,使显示为零。并使进料回转阀处于打开位置,出料回转阀处于关闭位置,启动出料输送设备及进料输送设备,此时物料通过进料口,进入1#计量仓,称重传感器受到物料的重力作用,随着物料的增加而输出电信号,并通过放大器进行放大,由PLC控制器进行采样后,输给计算机,当达到设定流量值后,计算机控制1#仓进料回转阀关闭,同时打开2#仓的进料回转阀,经延时后,打开1#仓出料回转阀,待物料放完后,自动关闭1#仓出料回转阀。2#计量仓重复1#计量仓的工作过程,这样使物料通过二个计量仓不断地连续计量及送料,达到对所输送物料的连续计量与控制。